Checklists are invaluable tools in manufacturing, serving as systematic guides to ensure that tasks are completed accurately, efficiently, and consistently. By utilizing checklists, manufacturers can streamline processes, minimize errors, and uphold quality standards throughout various stages of production.
In this blog, we'll explore nine widely used checklists in manufacturing, detailing their purposes, components, and benefits in enhancing operational efficiency and quality assurance.
Pre-Production Checklist
Purpose:
The pre-production checklist ensures that all necessary preparations are completed before initiating the manufacturing process, minimizing delays and ensuring smooth operations.
Components:
- Verification of raw material availability and quality
- Calibration and maintenance checks on machinery and equipment
- Confirmation of staffing requirements and training
- Review of production schedules and timelines
Benefits:
Machine Setup Checklist
Purpose:
The machine setup checklist ensures that manufacturing equipment is configured correctly and ready for operation, minimizing downtime and optimizing productivity.
Components:
- Verification of equipment cleanliness and condition
- Adjustment of settings and parameters for specific production requirements
- Installation and calibration of tooling, fixtures, and accessories
- Testing of safety features and emergency stops
Benefits:
- Reduces setup time and increases machine utilization
- Prevents errors and defects caused by incorrect machine settings
- Enhances operator safety and equipment reliability
Quality Inspection Checklist
Purpose:
The quality inspection checklist guides inspectors through the evaluation of finished products to ensure they meet specified quality standards and customer requirements.
Components:
- Examination of product dimensions, tolerances, and surface finish
- Testing of functional performance and reliability
- Inspection for defects, anomalies, and cosmetic imperfections
- Verification of labeling, packaging, and documentation accuracy
Benefits:
- Identifies defects and non-conformities before products reach customers
- Maintains consistency and uniformity in product quality
- Supports continuous improvement efforts through feedback and analysis
Preventive Maintenance Checklist
Purpose:
The preventive maintenance checklist outlines routine maintenance tasks to be performed on machinery and equipment to prevent breakdowns, prolong lifespan, and ensure reliability.
Components:
- Lubrication of moving parts and bearings
- Inspection and replacement of worn or damaged components
- Cleaning and calibration of sensors, actuators, and controls
- Verification of safety systems and interlocks
Benefits:
- Reduces unplanned downtime and production interruptions
- Extends equipment lifespan and reduces repair costs
- Improves operational safety and reliability
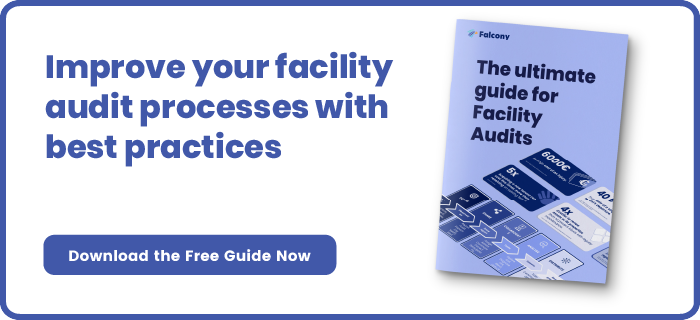
Safety Inspection Checklist
Purpose:
The safety inspection checklist helps identify and address potential hazards and safety concerns in the manufacturing environment to protect workers from accidents and injuries.
Components:
- Inspection of machine guards, safety interlocks, and emergency stops
- Assessment of electrical wiring, grounding, and isolation procedures
- Evaluation of housekeeping, slip/trip/fall hazards, and ergonomic risks
- Review of fire protection, emergency response, and evacuation procedures
Benefits:
Material Handling Checklist
Purpose:
The material handling checklist ensures safe and efficient handling, storage, and transportation of raw materials, components, and finished products within the manufacturing facility.
Components:
- Inspection of storage racks, shelves, and bins for stability and load capacity
- Verification of proper lifting techniques and use of mechanical aids
- Review of material labeling, identification, and traceability
- Assessment of material flow and inventory management processes
Benefits:
- Minimizes the risk of injuries and musculoskeletal disorders among workers
- Prevents damage, loss, or contamination of materials during handling and storage
- Optimizes material flow and inventory accuracy to support production schedules
Changeover Checklist
Purpose:
The changeover checklist guides operators through the process of transitioning production equipment from one product or batch to another efficiently and effectively.
Components:
- Cleaning and sanitizing equipment to prevent cross-contamination
- Adjustment of machine settings, tooling, and production parameters
- Verification of product specifications, labels, and packaging materials
- Testing and calibration of equipment to ensure proper operation
Benefits:
- Reduces changeover time and increases production flexibility
- Minimizes the risk of product mix-ups or quality issues during transitions
- Enhances operational efficiency and capacity utilization
Environmental Compliance Checklist
Purpose:
The environmental compliance checklist ensures that manufacturing activities adhere to environmental regulations, minimize pollution, and promote sustainable practices.
Components:
- Monitoring of air emissions, wastewater discharges, and hazardous waste generation
- Implementation of pollution prevention measures and waste reduction initiatives
- Compliance with permits, licenses, and reporting requirements
- Training on environmental responsibilities and emergency response procedures
Benefits:
Training and Certification Checklist
Purpose:
The training and certification checklist tracks employee training, qualifications, and certifications to ensure competency and compliance with job requirements and safety regulations.
Components:
- Documentation of training programs attended, dates, and results
- Verification of certifications, licenses, and permits required for specific job roles
- Assessment of skill proficiency, competency evaluations, and performance reviews
- Identification of training needs and development opportunities
Benefits:
- Ensures that employees possess the knowledge and skills necessary to perform their jobs safely and effectively
- Demonstrates compliance with regulatory training requirements and industry standards
- Supports career development and succession planning initiatives
Conclusion:
Utilizing these nine widely used checklists in manufacturing can significantly enhance operational efficiency, ensure quality assurance, and promote a safe and compliant work environment. By incorporating checklists into routine processes, manufacturers can streamline operations, minimize errors, and drive continuous improvement across all facets of production. Investing in effective checklist management systems and providing training on checklist utilization and best practices are essential for maximizing their effectiveness and achieving organizational goals.
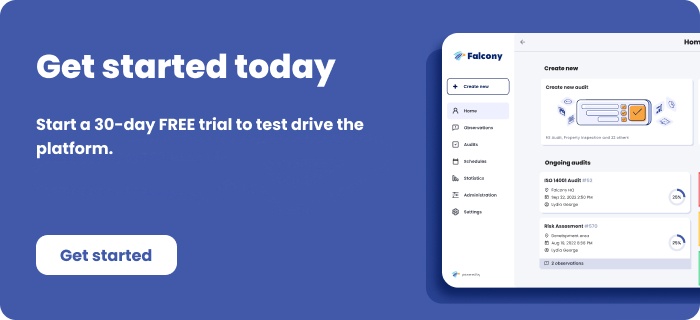
We are building the world's first operational involvement platform. Our mission is to make the process of finding, sharing, fixing and learning from issues and observations as easy as thinking about them and as rewarding as being remembered for them.
By doing this, we are making work more meaningful for all parties involved.
More information at falcony.io.