Checklists are indispensable tools in the chemical and petrochemical industry for ensuring compliance, safety, and operational efficiency.
These structured lists help personnel systematically verify equipment, processes, and procedures to identify potential issues and ensure adherence to standards and regulations. Here are ten different checklists commonly used in the chemical and petrochemical sector.
1. Pre-Startup Safety Review (PSSR) Checklist
The Pre-Startup Safety Review (PSSR) checklist is used before commissioning new equipment or processes to ensure that all safety, environmental, and operational requirements have been met. It covers aspects such as equipment integrity, safety systems testing, training completion, and regulatory compliance.
2. Process Hazard Analysis (PHA) Checklist
The Process Hazard Analysis (PHA) checklist is employed to identify, evaluate, and mitigate potential hazards associated with chemical processes. It includes techniques such as Hazard and Operability (HAZOP) studies, What-If analysis, and Failure Mode and Effects Analysis (FMEA) to assess process safety risks comprehensively.
3. Lockout/Tagout (LOTO) Checklist
The Lockout/Tagout (LOTO) checklist is used to ensure that energy sources are isolated and secured during maintenance, repair, or servicing of equipment to prevent accidental startup or release of hazardous energy. It verifies lockout/tagout procedures, equipment de-energization, and personnel training compliance.
4. Confined Space Entry Checklist
The Confined Space Entry checklist is utilized before entering confined spaces such as tanks, vessels, or pipelines to assess potential hazards and ensure safe entry and work conditions. It verifies atmospheric testing, ventilation, communication systems, rescue equipment availability, and adherence to entry procedures.
5. Permit-to-Work (PTW) Checklist
The Permit-to-Work (PTW) checklist is used to control hazardous work activities in chemical and petrochemical facilities. It verifies that all necessary permits, such as hot work permits, confined space entry permits, and excavation permits, have been obtained, and required safety measures are in place before commencing work.
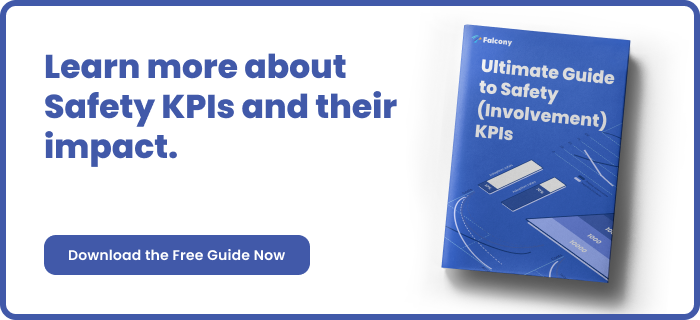
6. Chemical Storage Compatibility Checklist
The Chemical Storage Compatibility checklist ensures that chemicals are stored safely to prevent reactions, spills, or contamination. It verifies proper segregation of incompatible chemicals, adequate labeling, secondary containment measures, and compliance with storage requirements outlined in safety data sheets (SDS).
7. Emergency Response Checklist
The Emergency Response checklist is used to assess preparedness for responding to emergencies such as fires, chemical spills, or releases. It verifies the availability and functionality of emergency response equipment, communication systems, evacuation procedures, and personnel training.
8. Inspection and Testing Checklist
The Inspection and Testing checklist is employed to schedule and document routine inspections, maintenance activities, and equipment testing. It covers equipment integrity checks, calibration of instrumentation, preventive maintenance tasks, and compliance with regulatory requirements.
9. Personal Protective Equipment (PPE) Inspection Checklist
The Personal Protective Equipment (PPE) Inspection checklist is used to verify the condition and effectiveness of personal protective gear worn by employees. It covers inspection of gloves, safety goggles, respirators, hard hats, and protective clothing to ensure proper fit and functionality.
10. Environmental Compliance Checklist
The Environmental Compliance checklist assesses compliance with environmental regulations and permits governing chemical and petrochemical operations. It verifies wastewater discharge monitoring, air emissions controls, hazardous waste management practices, and environmental monitoring program adherence.
Conclusion
Checklists are indispensable tools for ensuring safety, compliance, and operational efficiency in the chemical and petrochemical industry. By employing various checklists tailored to specific processes, equipment, and regulatory requirements, organizations can systematically identify potential issues, implement corrective actions, and maintain a safe and environmentally responsible workplace. Incorporating checklists into routine operations fosters a culture of safety awareness and helps mitigate risks effectively in this high-risk industry.
If you're looking to implement a mobile tool for your audits, we've got you covered. Falcony | Audit is easy-to-use, fast to set up, has customisable workflows, vast integration possibilities and more. Contact us for more information.
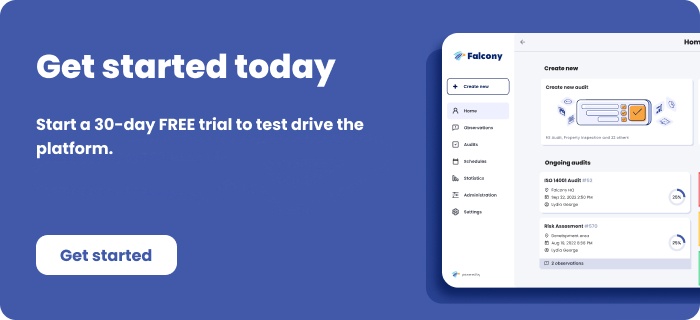
We are building the world's first operational involvement platform. Our mission is to make the process of finding, sharing, fixing and learning from issues and observations as easy as thinking about them and as rewarding as being remembered for them.
By doing this, we are making work more meaningful for all parties involved.
More information at falcony.io.