In logistics, meticulous planning and organization are essential to ensure smooth operations and timely delivery of goods. Checklists serve as invaluable tools for systematically reviewing, monitoring, and managing various tasks and processes within the supply chain.
Let's explore eleven of the most common checklists used in logistics and understand how they contribute to optimizing logistics operations:
Pre-Trip Inspection Checklist
Before embarking on a journey, drivers and carriers use pre-trip inspection checklists to ensure that vehicles are in optimal condition for transportation. This checklist typically includes items such as tire condition, fluid levels, brake systems, lights, signals, and cargo securing mechanisms.
Loading and Unloading Checklist
Loading and unloading checklists help warehouse personnel and drivers ensure the safe and efficient handling of goods during the loading and unloading process. This checklist covers aspects such as proper stacking, securing of cargo, weight distribution, use of handling equipment, and adherence to loading protocols.
Delivery Confirmation Checklist
Upon reaching the destination, delivery confirmation checklists are used to verify the accuracy and completeness of delivered goods. This checklist includes items such as matching the delivered items with the shipping manifest, inspecting for damages, obtaining recipient signatures, and documenting any discrepancies.
Inventory Replenishment Checklist
Inventory replenishment checklists are essential for maintaining optimal stock levels in warehouses and distribution centers. This checklist involves reviewing inventory levels, forecasting demand, generating purchase orders, coordinating with suppliers, and ensuring timely replenishment of stock.
Safety Compliance Checklist
Safety compliance checklists are used to ensure adherence to safety regulations and protocols within logistics facilities and during transportation. This checklist covers areas such as workplace safety practices, equipment maintenance, emergency procedures, hazard identification, and employee training.
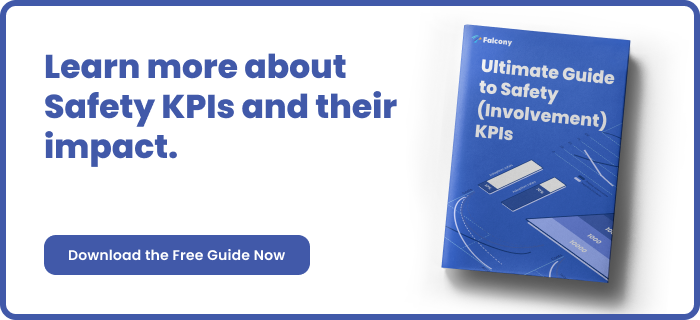
Quality Assurance Checklist
Quality assurance checklists are employed to uphold product quality standards throughout the supply chain. This checklist includes items such as product specifications, packaging integrity, labeling accuracy, cleanliness, product testing procedures, and compliance with quality assurance protocols.
Customs Documentation Checklist
Customs documentation checklists assist in ensuring compliance with customs regulations and requirements for international shipments. This checklist includes items such as accurate completion of customs forms, verification of tariff codes, inclusion of necessary documentation, and adherence to customs clearance procedures.
Route Planning Checklist
Route planning checklists help logistics planners optimize transportation routes for efficiency and cost-effectiveness. This checklist involves considering factors such as distance, traffic conditions, fuel consumption, vehicle capacities, delivery schedules, and route restrictions.
Cold Chain Management Checklist
Cold chain management checklists are vital for maintaining the integrity of temperature-sensitive goods during transportation and storage. This checklist includes monitoring temperature levels, ensuring proper refrigeration equipment operation, implementing temperature tracking systems, and responding to temperature deviations.
Vendor Qualification Checklist
Vendor qualification checklists are used to evaluate and select reliable suppliers and partners in the supply chain. This checklist includes assessing supplier capabilities, product quality, delivery reliability, financial stability, compliance with regulations, and adherence to contractual agreements.
Incident Response Checklist
Incident response checklists are crucial for handling unexpected events or emergencies during logistics operations. This checklist involves procedures for assessing risks, initiating response protocols, coordinating with relevant stakeholders, implementing contingency plans, and documenting incidents for review and improvement.
Conclusion
By implementing these checklists as part of their standard operating procedures, logistics companies can enhance efficiency, minimize risks, ensure compliance, and deliver superior service to their customers. Regular review, updates, and training on checklist usage are essential for maintaining effectiveness and adapting to evolving industry requirements and challenges.
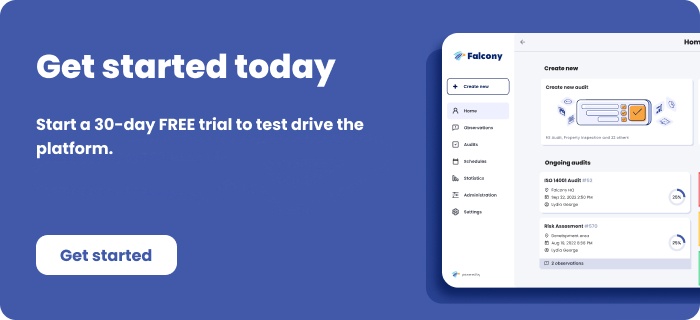
We are building the world's first operational involvement platform. Our mission is to make the process of finding, sharing, fixing and learning from issues and observations as easy as thinking about them and as rewarding as being remembered for them.
By doing this, we are making work more meaningful for all parties involved.
More information at falcony.io.