In today's rapidly evolving world, where technology, engineering, and innovation are driving forces, ensuring the reliability and safety of products and processes is paramount. One tool that plays a pivotal role in achieving this is the Failure Modes and Effects Analysis (FMEA). FMEA is a systematic approach used to identify, assess, and mitigate potential failures in various systems, products, or processes. In this blog post, we will delve into the details of FMEA, its purpose, benefits, and how it is conducted.
What is FMEA?
Failure Modes and Effects Analysis (FMEA) is a structured methodology employed to identify and prioritize potential failure modes in a system, product, or process. The primary goal of FMEA is to anticipate potential issues, assess their potential impact, and develop strategies to prevent or mitigate them. By proactively addressing potential failures, FMEA helps improve reliability, safety, and overall performance.
The Components of FMEA
1. Failure Modes
Failure modes are the cornerstone of the FMEA process. They represent the various ways in which a system, product, or process could fail to meet its intended function or performance. These failures can range from simple malfunctions to critical breakdowns with severe consequences. For example, in an automotive braking system, failure modes could include brake fluid leakage, brake pad wear, or complete brake system failure. By comprehensively identifying these failure modes, teams can later analyze their potential effects and devise strategies to mitigate them effectively.
2. Effects
The effects of failure modes describe the consequences that arise when a specific failure occurs within a system, product, or process. These effects encompass a wide range of outcomes, such as safety hazards, operational disruptions, financial losses, environmental impacts, and even reputational damage. For instance, if a failure mode in a medical device involves inaccurate readings, the effect could lead to misdiagnosis and potential harm to patients. Understanding and evaluating these effects allow teams to prioritize their efforts towards preventing the most critical failures that could have severe repercussions.
3. Risk Ranking
One of the key objectives of FMEA is to prioritize which failure modes require immediate attention and mitigation. This is achieved through the risk ranking process, which involves assigning ratings to the severity, occurrence, and detection of each failure mode:
-
Severity Rating: This rating quantifies the potential impact of a failure mode's effect. A high severity rating indicates a failure mode with significant consequences, while a low rating implies minimal impact.
-
Occurrence Rating: Occurrence rating reflects the likelihood of a failure mode happening. A high occurrence rating suggests that a failure mode is more likely to occur, while a low rating signifies a lower likelihood.
-
Detection Rating: Detection rating gauges the likelihood of detecting a failure mode before it leads to harmful consequences. A low detection rating implies that a failure mode is challenging to detect early, while a high rating indicates good detectability.
These three ratings are multiplied together to calculate the Risk Priority Number (RPN) for each failure mode. The RPN serves as a numerical indicator of the overall risk associated with a specific failure mode, helping teams prioritize mitigation efforts. High RPN values indicate failure modes with a higher level of risk, necessitating immediate attention, while lower RPN values may warrant lesser priority.
By thoroughly analyzing failure modes, assessing their effects, and quantifying their risk through the RPN, FMEA enables teams to focus on the most critical issues and allocate resources efficiently to ensure the reliability and safety of the system, product, or process in question.
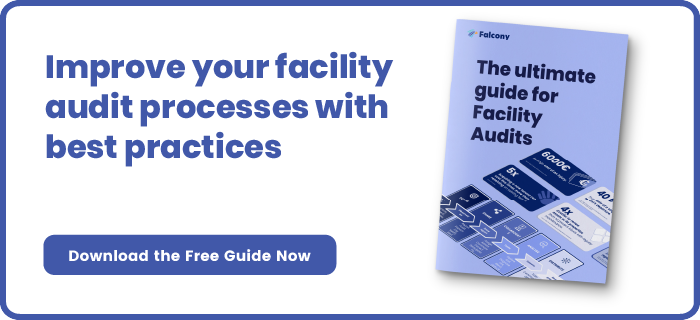
The FMEA Process
1. Select the System or Process
Choosing the appropriate system, product, or process for FMEA is a crucial first step. This selection should be based on factors such as complexity, criticality, and potential impact. The scope of the analysis should be clearly defined to ensure that the FMEA team can effectively identify and evaluate all relevant failure modes. Whether it's an intricate manufacturing process, a complex software application, or a safety-critical device, selecting the right subject for analysis lays the foundation for a successful FMEA.
2. Assemble a Cross-Functional Team
FMEA is most effective when conducted by a diverse team of experts representing various disciplines related to the chosen system or process. This cross-functional approach brings together individuals with different perspectives, experiences, and skill sets. Engineers, designers, quality control specialists, safety professionals, and even end-users might be part of this team. Their collective knowledge contributes to a comprehensive analysis that considers different aspects and potential failure scenarios that might otherwise be overlooked.
3. Identify Failure Modes
Brainstorming and identifying potential failure modes is a collaborative effort within the FMEA team. This creative process involves thinking critically about how each component, interaction, or step in the system could go wrong. During this phase, no idea is too small or insignificant. The goal is to generate a comprehensive list of potential failure modes, which will serve as the foundation for the subsequent analysis.
4. Assign Severity, Occurrence, and Detection Ratings
This step involves assigning quantitative ratings to each failure mode based on three key factors:
-
Severity: Evaluate the potential impact of the failure mode's effect. A high severity rating is given to failure modes with severe consequences, while a low rating is assigned to those with minor effects.
-
Occurrence: Assess the likelihood of the failure mode occurring. A high occurrence rating is assigned to failure modes that are more likely to happen, while a low rating indicates lower likelihood.
-
Detection: Gauge the probability of detecting the failure mode before it leads to harmful effects. A low detection rating reflects poor detectability, while a high rating indicates a high likelihood of timely detection.
Assigning these ratings requires a combination of technical expertise, historical data, and critical thinking. Collaboration within the cross-functional team is vital to ensure a well-rounded assessment.
5. Calculate Risk Priority Number (RPN)
The Risk Priority Number (RPN) is a numerical value obtained by multiplying the severity, occurrence, and detection ratings for each failure mode. The RPN provides a quantitative measure of the overall risk associated with a specific failure. Higher RPN values indicate higher potential risk. This step helps prioritize which failure modes require immediate attention and mitigation efforts.
6. Prioritize and Implement Mitigation Strategies
Based on the calculated RPN values, the team can prioritize which failure modes demand the most immediate attention. Higher RPN values highlight areas of potential concern that warrant thorough mitigation strategies. The team then collaboratively devises and implements strategies to address these failure modes. These strategies could involve design changes, process improvements, additional testing, redundancy implementation, or procedural modifications.
7. Review and Update
FMEA is not a one-time process. As systems, products, and processes evolve, new failure modes can emerge, and the impact of existing ones may change. Regular reviews and updates to the FMEA ensure that it remains effective in managing risks over time. This iterative approach allows organizations to stay proactive and agile in addressing potential failures and maintaining the reliability and safety of their offerings.
The FMEA process is a dynamic and continuous effort that fosters a culture of preventive risk management and quality improvement. By following these steps diligently, organizations can enhance their ability to deliver reliable and safe products, systems, and processes to their customers and stakeholders.
Benefits of FMEA
1. Risk Reduction
One of the primary advantages of implementing Failure Modes and Effects Analysis (FMEA) is its significant contribution to risk reduction. By systematically identifying potential failure modes and their associated effects, organizations can proactively devise strategies to mitigate or eliminate these risks. This preventive approach helps prevent costly and potentially catastrophic failures from occurring in the first place. By addressing vulnerabilities early on, FMEA enables companies to enhance the reliability of their products, systems, and processes, leading to increased customer satisfaction and trust.
2. Enhanced Reliability
FMEA is a cornerstone of reliability engineering. It empowers organizations to focus on areas where the risk of failure is high and the potential consequences are severe. Through careful analysis and risk assessment, organizations can make informed decisions regarding design improvements, process modifications, and quality control measures. This targeted approach not only reduces the likelihood of failures but also enhances the overall reliability of the product or process, thereby extending its operational lifespan and minimizing costly downtime.
3. Informed Decision-Making
Effective decision-making requires access to accurate and comprehensive information. FMEA provides organizations with a wealth of insights into potential failure scenarios, their impacts, and the likelihood of occurrence. Armed with this knowledge, decision-makers can allocate resources efficiently, prioritize projects, and invest in the areas that are most critical to the organization's success. In a competitive business environment, informed decisions driven by FMEA can lead to a competitive advantage and improved overall performance.
4. Cost Savings
While the initial investment in conducting FMEA might seem significant, the long-term cost savings it offers are substantial. By addressing potential failures before they occur, organizations can avoid expenses associated with recalls, repairs, legal liabilities, and even potential lawsuits. Additionally, preventing production disruptions due to unexpected failures can lead to improved operational efficiency and reduced downtime. Overall, the proactive nature of FMEA helps organizations save both time and money by mitigating risks and reducing the impact of failures on their bottom line.
5. Continuous Improvement
FMEA is not a one-time process; it's an ongoing commitment to quality and improvement. As organizations gather more data and insights, they can refine their FMEA processes and continuously enhance their risk assessment capabilities. This culture of continuous improvement promotes a proactive mindset within the organization, fostering an environment where employees are encouraged to identify and address potential issues before they escalate. Over time, this approach can lead to a higher level of organizational resilience and adaptability.
6. Regulatory Compliance and Reputation
In industries where safety, reliability, and quality are paramount (such as healthcare, aerospace, and automotive sectors), adhering to regulatory standards is crucial. FMEA provides a structured methodology for demonstrating compliance with these standards. Moreover, organizations that consistently employ FMEA to ensure the safety and reliability of their products and processes enhance their reputation in the market. Building a reputation for delivering high-quality, reliable, and safe products can lead to increased customer loyalty and positive brand recognition.
Conclusion
In conclusion, Failure Modes and Effects Analysis (FMEA) is a powerful tool that offers a range of significant benefits to organizations across various industries. From reducing risks and enhancing reliability to enabling informed decision-making and cost savings, FMEA is a cornerstone of effective risk management and continuous improvement. By systematically identifying and mitigating potential failures, organizations can build products, systems, and processes that meet the highest standards of quality, safety, and reliability.
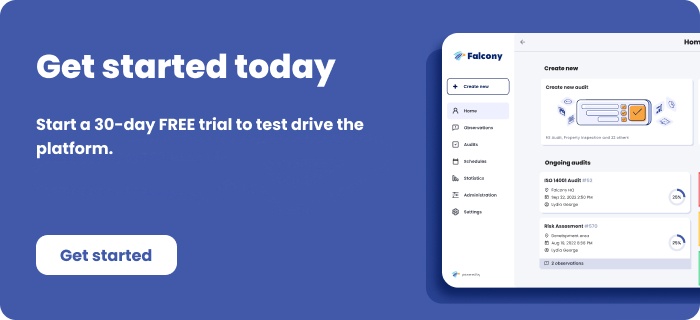
We are building the world's first operational involvement platform. Our mission is to make the process of finding, sharing, fixing and learning from issues and observations as easy as thinking about them and as rewarding as being remembered for them.
By doing this, we are making work more meaningful for all parties involved.
More information at falcony.io.