In the dynamic and competitive landscape of logistics, efficiency and precision are paramount. To achieve optimal performance, some businesses in the logistics sector have turned into Lean Six Sigma methodologies. Combining the principles of Lean, which focuses on waste reduction and process flow, with the data-driven approach of Six Sigma, which targets process variations and defects, can result in significant improvements in logistics operations. In this blog post, we will explore how to effectively implement Lean Six Sigma in logistics to enhance efficiency, reduce costs, and exceed customer expectations.
Define the Project Scope
Before embarking on any improvement initiative, define the specific logistics process that requires attention. This could be inbound transportation, order processing, warehousing, outbound distribution, or any other aspect of the supply chain. Clearly articulate the goals you want to achieve through this project, whether it's reducing lead times, lowering transportation costs, improving order accuracy, or enhancing overall efficiency.
Map the Current Process
Create a comprehensive process map that illustrates the current flow of the chosen logistics process. Include every step, decision point, interaction, and handoff. This visual representation helps you understand the process intricacies, identify bottlenecks, redundancies, and inefficiencies. It serves as a baseline against which you can measure the impact of your improvements.
Identify Waste
Applying Lean principles, categorize the types of waste present in the process. Waste can manifest as unnecessary waiting times during transportation or handling, excess inventory holding costs, overproduction due to inaccurate demand forecasts, unnecessary movement of goods within the warehouse, or inefficient use of human resources. By categorizing waste, you gain clarity on areas needing attention.
Measure Performance
Collect relevant data to quantify the performance of the current logistics process. Metrics can include cycle times (the time it takes for an order to be fulfilled), lead times (the time from order placement to delivery), order accuracy rates, inventory turnover, and customer satisfaction scores. These metrics provide a factual basis for analysis and improvement.
Analyze and Identify Root Causes
Leverage Six Sigma tools like root cause analysis, fishbone diagrams, and Pareto charts to delve into the reasons behind process inefficiencies or defects. Identify the root causes that contribute to these issues. For instance, if late deliveries are a problem, dig into whether it's due to poor route planning, communication breakdowns, or other factors.
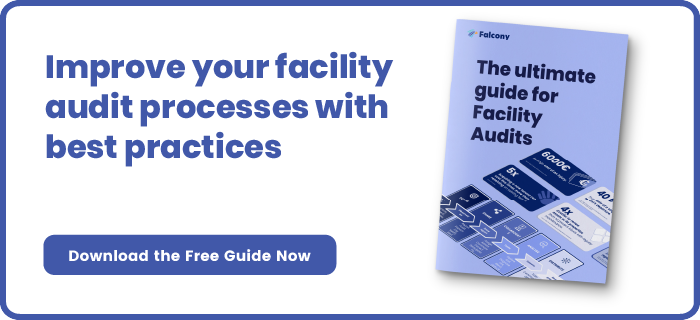
Design Improvements
Based on the analysis, brainstorm and design improvements that address the identified root causes. For instance, if inventory holding costs are high due to inaccurate demand forecasting, consider implementing better demand prediction tools or optimizing your replenishment strategy. The improvements could range from process changes to technology adoption or resource reallocation.
Implement Changes
Carefully implement the proposed improvements, ensuring that all relevant stakeholders are aligned and informed. This might involve revising standard operating procedures, deploying new technology, training staff on the updated processes, or adjusting communication protocols with suppliers and partners.
Standardize Processes
Document the improved procedures and processes in detail. Create standardized work instructions, guidelines, and checklists that outline the steps to be followed. Standardization ensures that the newly optimized logistics process is consistently executed, reducing variability and minimizing the chances of errors.
Measure and Monitor
After implementing the changes, measure the updated performance metrics to quantify the improvements. Compare these metrics to the baseline data collected earlier. Continuously monitor these metrics to ensure the gains are sustained and to identify any anomalies that might require corrective actions.
Continuously Improve
Lean Six Sigma is a continuous improvement journey. Schedule regular reviews to assess the effectiveness of the changes and gather feedback from the involved teams. This proactive approach ensures that you remain agile and adaptable to the evolving demands of the logistics landscape, consistently seeking out opportunities for further optimization.
Conclusion
Utilizing Lean Six Sigma principles in logistics can be transformative, enabling businesses to streamline their processes, enhance customer satisfaction, and gain a competitive edge in the market. By diligently following these steps, you're not just solving immediate issues; you're creating a culture of continuous improvement that positions your logistics operations for long-term success.
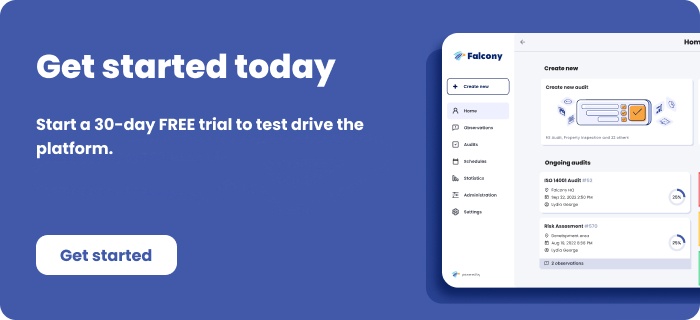
We are building the world's first operational involvement platform. Our mission is to make the process of finding, sharing, fixing and learning from issues and observations as easy as thinking about them and as rewarding as being remembered for them.
By doing this, we are making work more meaningful for all parties involved.
More information at falcony.io.