In my last blog post, titled “HSEQ in a Manufacturing Facility: This is what you should check”, I covered important areas that can help you improve the HSEQ management of your manufacturing facility. However, to help you to create an efficient workplace you need to know about the 5S system.
What is 5S?
5S is system developed for lean management in manufacturing. 5S is a helpful tool for you to use to organise your workplace, as well as to make production and HSEQ checks easier in the future. By improving your quality, you reduce waste, which increases profit.
While 5S was born in Japan, it has been implemented by several companies around the world. The 5 S's stand for: seiri (sort), seiton (set), seiso (shine), seiketsu (standardise), and shitsuke (sustain). To make it easier to understand, I will use the English version of the S’s in this blog.
1. Sort
As you can likely tell from its name, this S refers to sorting out of your work stations. Simply remove all unnecessary clutter and waste that doesn’t need to be there. To help you clear out your space, you can add tags on the articles that need to be discarded. This way, you prevent issues in the future.
2. Set
This S is also known as “set-in-order”, and focuses on organisation.
This S helps you organise your work tools and label them so that you and your employees know where they belong after being used. This will allow you to experience higher levels of efficiency since everyone knows where items are.
3. Shine
This S will help you make sure that all of your materials and equipment are shining clean at the end of every work day and during workplace inspections. By ensuring that your workplace is clean, you can limit health hazards for your employees and improve safety for everyone at work. This also reduces the risk of accidental production quality faults.
4. Standardise
This S is for routine. Standardise who is responsible for cleaning, sorting and setting things in order for every employee. You can make a checklist of responsibilities that has a schedule of what tasks needs to be done by a certain time, and assign them to your employees. That way, everyone is responsible for ensuring an organised and clean workplace.
5. Sustain
This S is for long-term goals. Make 5S an integrated part of your company strategy inside of production management, safety walks and HSEQ checks. You will find that you and your employees will know where things are and when equipment was last cleaned. Everyone will also be on top on checks coming up in the future. This S, therefore, is an integral part of internal communications. It will help you and your employees communicate efficiently to ensure the organisation and cleanliness of the workstations.
Final Thoughts
By implementing 5S, you are proactively engaging everyone in the company to take responsibility for order, HSEQ checks, and production checks.
As mentioned last time, the most important element of success in your company are the people. When you engage them in 5S maintenance, you give them a purpose in the company which includes more than just their job function. That will provide you with happier employees who want to do their best to make the company a safer place to work.
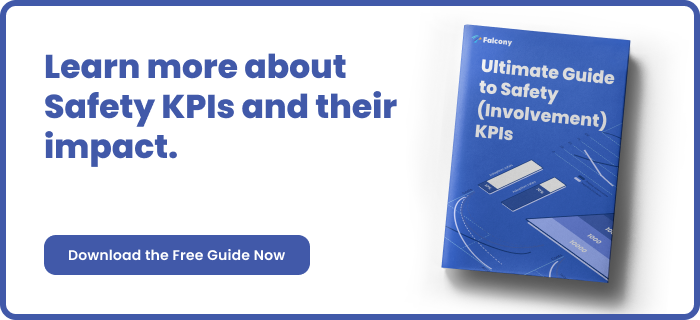
We are building the world's first operational involvement platform. Our mission is to make the process of finding, sharing, fixing and learning from issues and observations as easy as thinking about them and as rewarding as being remembered for them.
By doing this, we are making work more meaningful for all parties involved.
More information at falcony.io.