10 Most common safety incidents in logistics
The logistics industry plays a pivotal role in supply chains around the world, ensuring goods reach their destinations efficiently. However, this sector is not without its safety challenges. Recognizing and addressing common safety incidents is essential to protect workers, assets, and the smooth functioning of operations. Let's delve into the 10 most frequent safety incidents in logistics and explore strategies for prevention:
1. Slips, Trips, and Falls
These seemingly mundane incidents account for a significant number of workplace injuries. Uneven flooring, wet surfaces, and poorly maintained walkways contribute to slips, trips, and falls. Regular housekeeping practices, such as promptly cleaning spills, repairing damaged flooring, and maintaining clear walkways, are crucial. Additionally, promoting a culture of awareness among employees can significantly reduce the occurrence of these incidents.
2. Forklift Accidents
Forklifts are essential for material handling, but they also pose significant risks. Collisions with other vehicles or structures, tip-overs due to unbalanced loads, and unsafe driving practices can lead to accidents. Proper training and certification for forklift operators, regular maintenance checks, clearly marked traffic lanes, and cautious speed limits within facilities are vital measures to prevent these incidents.
3. Manual Handling Injuries
Lifting and carrying heavy loads without proper techniques can result in musculoskeletal injuries. Educating workers about ergonomic lifting practices, using mechanized lifting aids whenever possible, and implementing regular stretching routines can significantly reduce the risk of manual handling injuries.
4. Vehicle Collisions
Vehicle accidents can occur both within logistics facilities and on the road. Distracted driving, fatigue, and inadequate vehicle maintenance are common causes. Implementing strict guidelines on safe driving practices, scheduling regular maintenance checks, and promoting driver awareness campaigns are essential steps to prevent collisions.
5. Falling Objects
Falling objects from shelves, racks, or conveyor systems can cause injuries. Adequate storage procedures, such as proper stacking, secure shelving units, and using safety nets, can prevent objects from falling. Regular inspections and reinforcement of storage protocols are crucial to prevent these incidents.
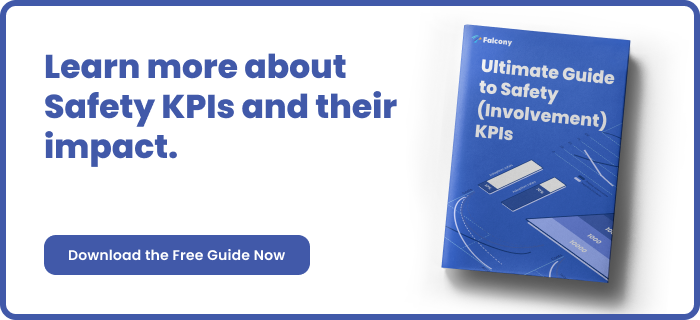
6. Loading and Unloading Accidents
Loading and unloading materials from trucks and containers can be hazardous. Accidents can occur due to improperly secured loads or miscommunication between workers. Providing proper training to loading and unloading personnel, using appropriate equipment for lifting and securing loads, and implementing clear communication protocols can prevent accidents during these processes.
7. Confined Space Hazards
Confined spaces present unique risks due to limited ventilation and potential exposure to hazardous gases. Strict adherence to confined space entry protocols, proper ventilation, and continuous air quality monitoring are essential to prevent incidents within such spaces.
8. Chemical Spills and Exposure
Mishandling of hazardous chemicals during transportation or storage can lead to spills and exposure risks. Thorough training on proper chemical handling, regular equipment inspections, and the use of appropriate PPE can minimize the potential for chemical incidents.
9. Electrical Accidents
Electrical incidents can result from faulty equipment, improper wiring, or unsafe practices. Regular electrical system inspections, compliance with safety codes, and proper training in electrical safety protocols can significantly reduce the risk of electrical accidents.
10. Fire and Emergency Incidents
Fires, smoke, and other emergencies can disrupt logistics operations and jeopardize worker safety. Regularly testing fire suppression systems, conducting emergency response drills, and ensuring that employees are well-trained in emergency procedures are critical measures to prevent and manage such incidents.
Conclusion
By addressing these common safety incidents head-on, the logistics industry can create a safer working environment for all stakeholders. Ongoing training, a commitment to enforcing safety protocols, regular equipment maintenance, and fostering a culture of safety awareness are the building blocks of a secure logistics operation. Ultimately, prioritizing safety not only protects workers but also contributes to smoother operations, reduced downtime, and enhanced overall efficiency in the logistics industry.
Are you looking for a tool to monitor nonconformities or any other issues in your organisation? Falcony | Observe ticks all the boxes for issue management, is easy to customise, enables real dialogue and is a lot more.
We are building the world's first operational involvement platform. Our mission is to make the process of finding, sharing, fixing and learning from issues and observations as easy as thinking about them and as rewarding as being remembered for them.
By doing this, we are making work more meaningful for all parties involved.
More information at falcony.io.

Related posts
How to create a culture of safety involvement and reporting?
Safety in any environment, particularly one as intricate and dynamic as the aviation industry, is a...
Training your mind to associate safety in the workplace with reporting
Workplace safety is a paramount concern for organizations across all industries. Ensuring a safe...
8 Most Common Safety Incidents in Real Estate and Property Management
In the realm of real estate and property management, safety is not merely a regulatory obligation...